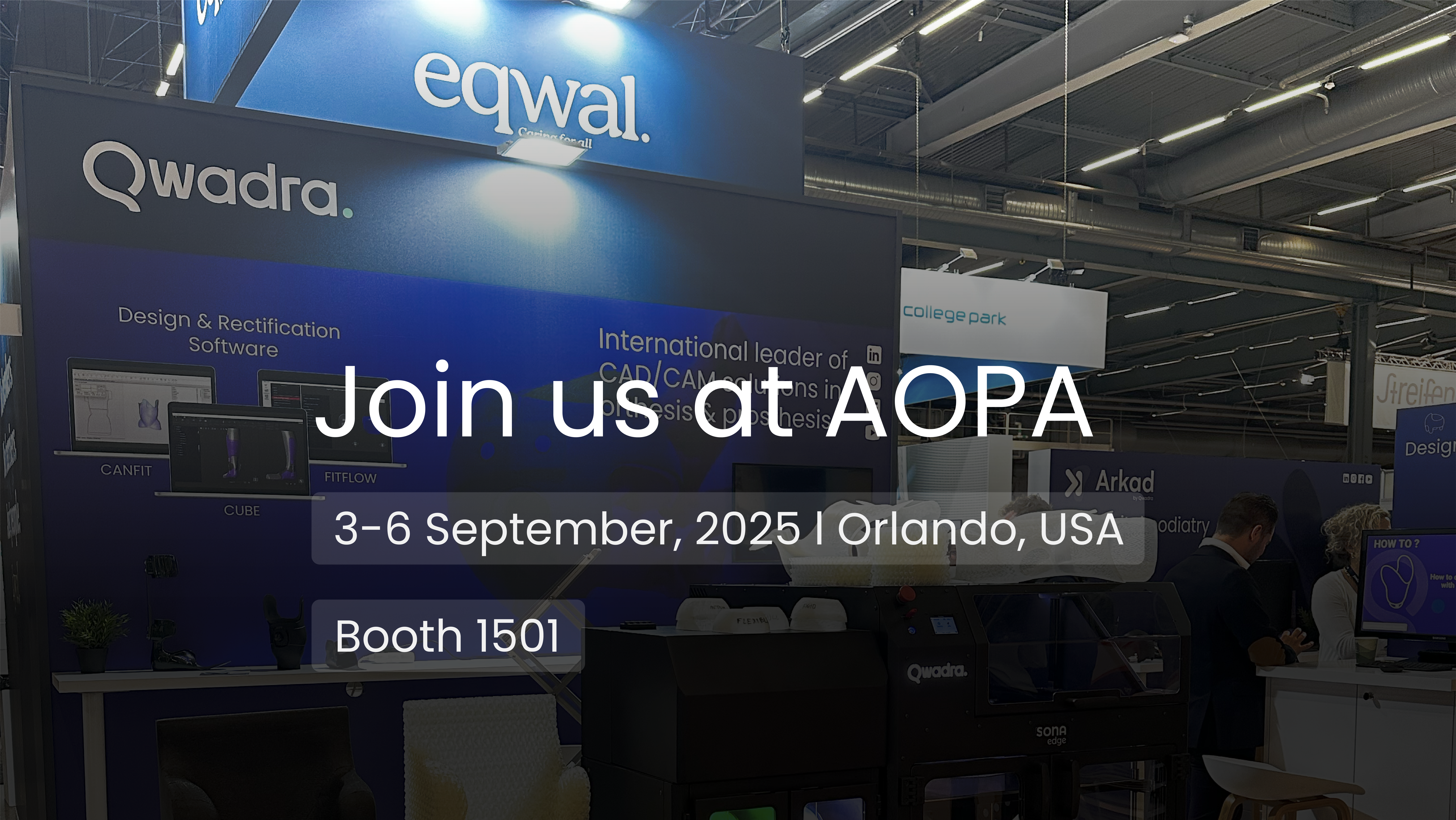
- Events
Qwadra at AOPA 2025: driving innovation in O&P with digital solutions
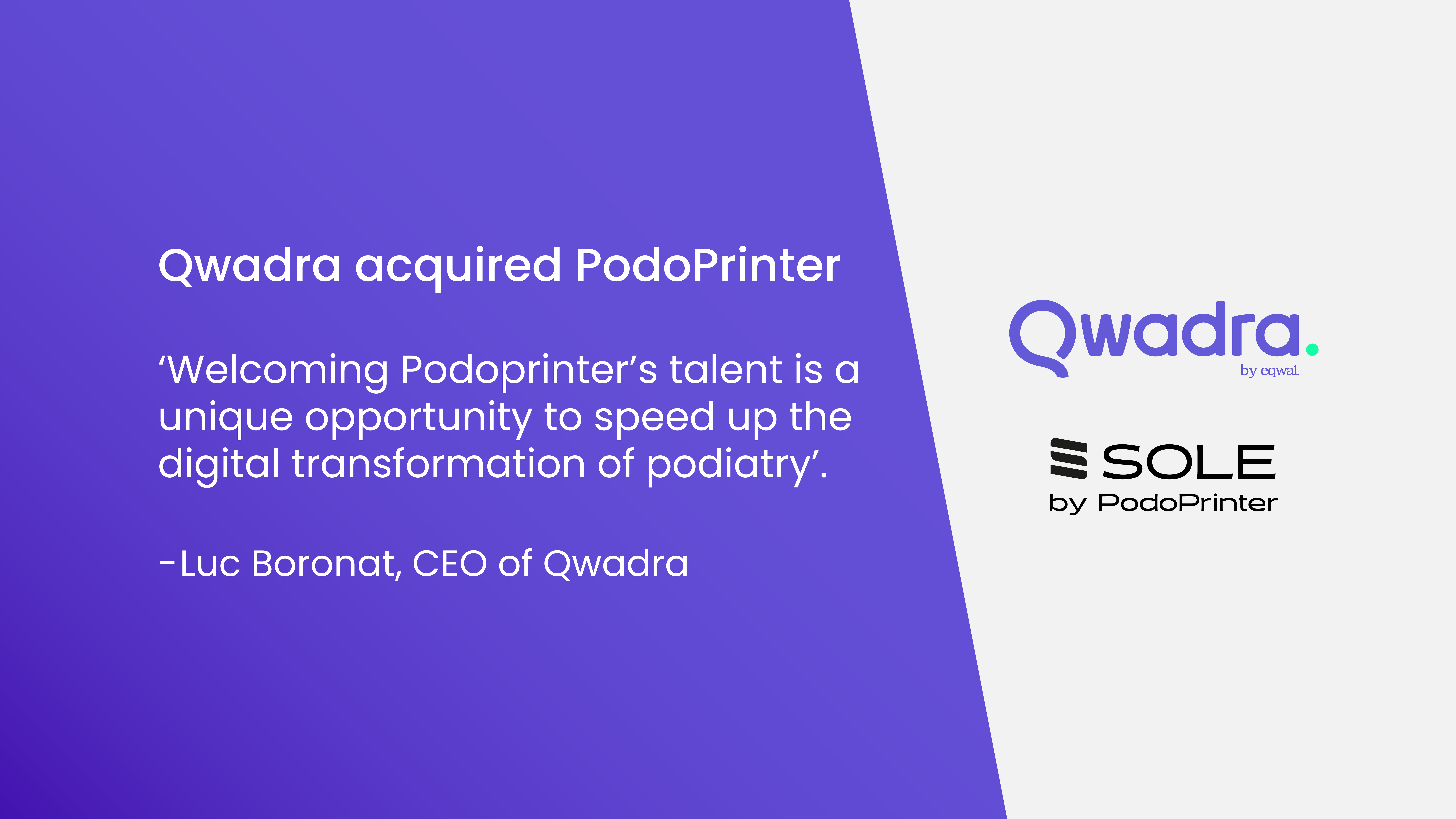
- Events
Qwadra acquires PodoPrinter: accelerating the digital future of podiatry
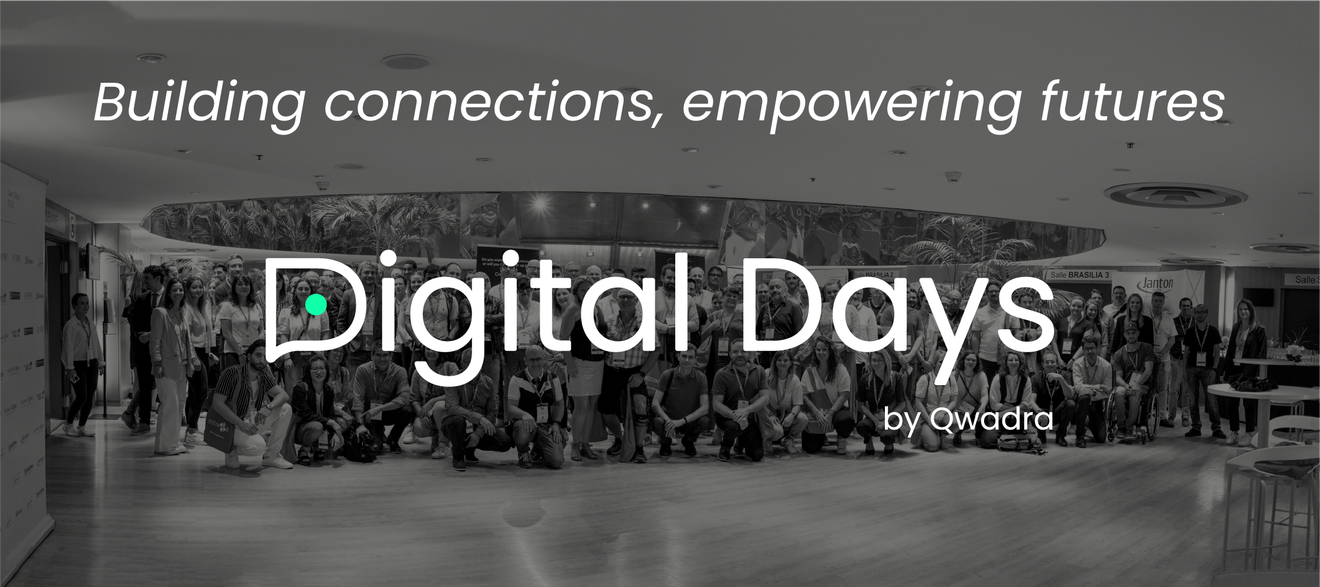
- Events
Qwadra Digital Days 2025: Shaping the future of O&P
Today, we’re proud to highlight the expertise of Arthur Bertet, Certified Prosthetist-Orthotist at Lagarrigue – France, who leveraged a fully digital workflow featuring our CaptviaPlus 3D scanner, Cube design software and the newly released Sona Flex 3D printer, built for seating orthoses to dramatically improve the quality of life of Malorie, a 20-year-old paraplegic patient.
This dual-perspective interview explores both the CPO decision-making behind this technology-driven process and its real-world impact, as experienced by Malorie herself.
Malorie’s treatment called for a highly customized seating corset. As a paraplegic since early childhood, prolonged sitting caused significant discomfort, and a chronic bedsore had become a growing concern. For the CPO Arthur Bertet, the challenge was clear: create a device that provided support, pressure relief and long-term comfort – all while minimizing weight and bulk.
Using the CaptviaPlus 3D scanner, Arthur Bertet captured an accurate impression of Malorie’s posture. The scan was then imported into Cube software, where he designed the perfect fitted device to her. This digital workflow ensured a high level precision and reliability.
The result? A perfectly seating device, ready for 3D printing on the Sona Flex, our new advanced 3D printer optimized for seating devices.
The Sona Flex was specifically designed to address the limitations of traditional seat fabrication.
For Arthur Bertet, one of the key advantages was the ability to vary material density with precision across very short distances. This level of control allowed him to tailor the stiffness and flexibility of the seat exactly where needed, enhancing both pressure relief and comfort for the patient.
Thanks to the fidelity of the Sona Flex, the final product remained true to the initial CAD design according to Arthur Bertet, preserving every detail defined during the digital rectification process. This precision played a direct role in Malorie’s improved comfort and the successful healing of a difficult bedsore that had previously resisted treatment.
Finally, the ecological benefits of the technology stood out. Traditional manufacturing methods often generate significant material waste, whether from foam blocks or plastic shells. In contrast, Sona Flex prints only what is needed.
As Arthur put it, “With this 3D printing digital seat technique, we no longer have this problem. We have zero waste, we only use the material we need to make the seat.”
Malorie’s experience with her new 3D-printed seating device extends far beyond the clinical benefits – it has transformed her day-to-day comfort and independence.
One of the most noticeable improvements was the weight of the orthosis. Being significantly lighter than her previous seat. She also appreciated the breathability of the device. Unlike traditional shells that trap heat and cause discomfort – particularly in the summer, the mesh structure of the 3D-printed seat allows for airflow, helping her stay cool and reducing the risk of skin irritation. Another major plus was the ease of maintenance: the entire seat is fully washable, which made a world of difference in terms of hygiene and practicality.
Her verdict? “Yes, I would definitely recommend it to other patients. The difference in comfort and usability is clear.” – Malorie Debaire.
Malorie’s story exemplifies how digital technologies can be used not only to improve clinical precision, but to profoundly impact lives. As the O&P profession continues to embrace digital transformation, digital tools are enabling CPOs such as Arthur Bertet to deliver care that’s more efficient and more effective than ever before.